Internship Project
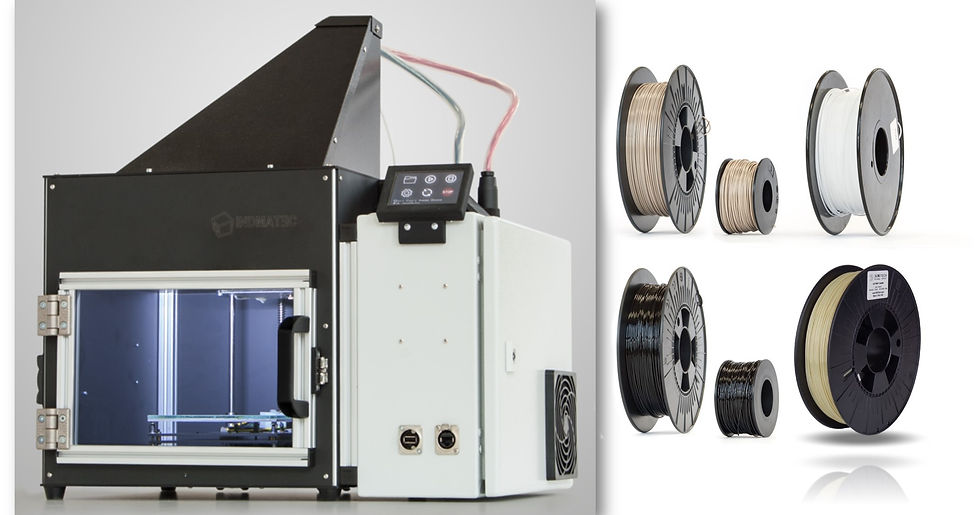
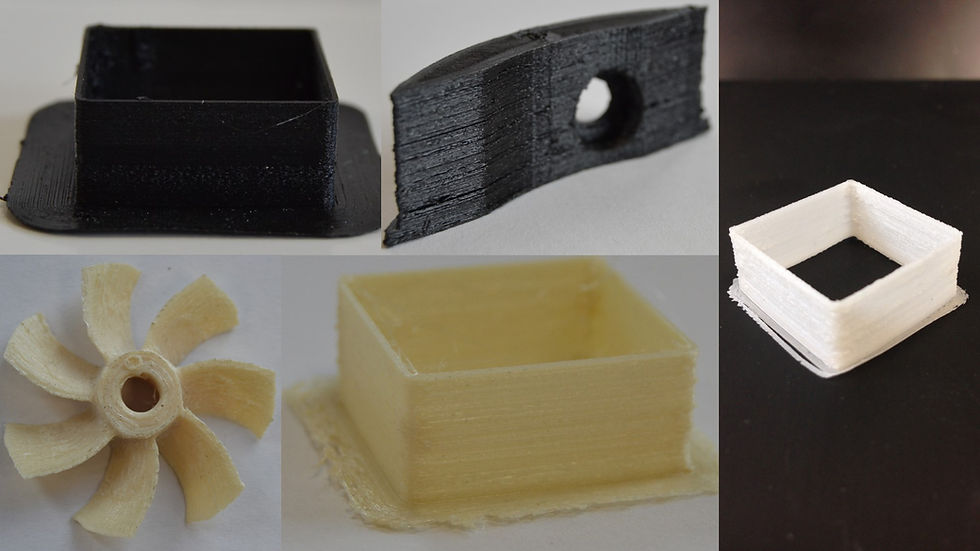

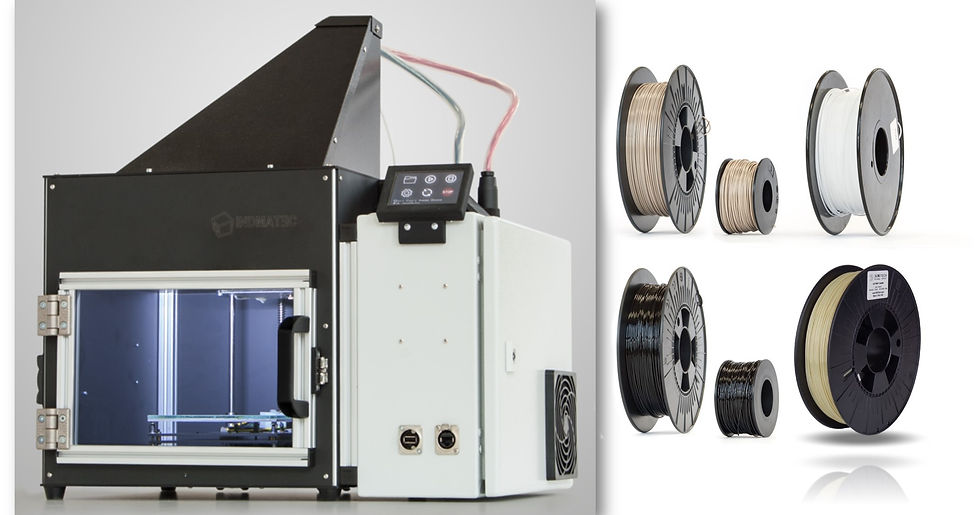
Determination of the printing parameters of ULTEM 9085, ULTEM 1000 and POM-C for the company's FDM printer.
During my internship at Apium Additive Techonologies GmbH at Karlsruhe, Germany, I had to do a project for my university to present as a final thesis.
Apium Additive Technologies’s printer HPP 155 was specially designed to print PEEK. But back in 2016, one of the company’s goal was to go even further and be able to print other materials with the same quality as they can print PEEK. Along with the FDM printer, they also offer several filaments for FDM 3D printing such as POM-C, PEI-ULTEM 9085 and ULTEM 1000.
​
That's where my project comes in. Besides the common tasks in the R&D laboratory, I worked in this project along a fellow intern, named Sasidhar Gorantla. We used Simply3D software for the slicing and G-Code generation.
The methodology for the project was the following:
1.Research about the material properties and their use with FDM printers, to estimate a set of initial printing parameters.
2.Test the initial parameters to print simple parts with the materials.
3.We decided to print probes according to the ASTM D-638 Type V, which is used to test plastics and metals without complete filling. Our objective was to print probes of 50%, 75% and 100% infill, with a 0.1mm, 0.2mm and 0.3mm layer height. We kept printing and changing parameters till good visual results were obtained.
4.Once the previous objective was accomplished, we headed to the KIT Laboratory to make a tensile test of every probe printed, for which we have 3 samples of each type of probe.
5.The tensile test results were analysed and compared with the mechanical properties of the same material after injection molding.
The results were basically that all materials parts made with the FDM printer reached the 78% of the maximum stress of injection molding parts. The POM-C behaved really great along all the testing and didn’t show any disadvantages, for all the layer heights and infill percentage. On the other side, the ULTEM 9085 proved to be significantly easy to handle and showed excellent results for all the layer heights and infill percentages, which was not the case for the ULTEM 1000.