CFD Analysis
Flow Cases Studied
After I finished with my last course at my university in March 2017, I started working individually with my previously Fluid Mechanics Professor, Dr. Armando Blanco, who is in charge of several thesis and projects related to CFD in the Fluid Mechanics Laboratory of the university. Working those four (4) months with him, I learned how to run Computational Fluid Dynamics studies of several cases of flow. The programs I used were the following:
​
-SALOME for Geometry Generation, Meshing and Post-Processing.
-Code Saturne for CFD Calculations.
-SYRTHES for Heat Transfer Calculations.
​
All of the softwares were used in an Ubuntu environment. This softwares were used because they have the advantage of being open-software ones. The specific cases I studied were the folowing:
I created the geometry for a 2D study, and the hexahedral mesh with different mesh refinement in the X, Y and Z directions using SALOME. I set up a steady-state, viscous, laminar, isothermal, constant properties fluid CFD simulation with non-slip walls, a moving wall, and symmetry planes with Code Saturne and Salome mesh previously created. After examination of the output and results files with monitoring points, the results were analyzed in SALOME.
April-July 2017
2. Flow in a 2D channel
This is a simple case of a laminar flow along a 2D channel, but it is of high importance because when there is a flows along a 2D channel, with a relatively low velocity, a hydraulic stable status can be achieved after a certain distance. This stable flow status is named as hydraulically fully developed flow.
​
That is why this case was one of the first ones I studied. For the CFD calculation, I created a simple geometry and mesh using SALOME, with a dense mesh near the inlet and the walls of the duct.
3. Step flow
The flow over a backward facing step is a good flow case to study the separation and reattachment of turbulent flows, which occur in many practical engineering applications.
​
The CFD domain used for this case consists of inlet, backward facing step and an outlet. A developed steady turbulent flow enters through the inlet, passes over the step where it detaches from the boundary and further reattaches at a particular length. First, the study was made for a laminar, steady flow.
This simplified-nuclear vessel case was studied in two parts:
​
I. Simple Junction: I used an oversimplified 2D junction including an inlet, an outlet, walls and symmetries, where the flow enters through a hot inlet into a cold environment and then exits. This geometry is a very rough approximation of the cold branch and the downcomer of the vessel in a nuclear pressurized water reactor. The effect of temperature on the fluid density was not taken into account in this part. A steady, laminar flow was considered for the CFD simulation.
​
II. Full Domain: The complete fluid domain represents very roughly elements of a nuclear pressurized water reactor vessel. For this case I merged separate meshes into a single fluid domain, with Code Saturne features for mesh joining and hanging nodes. This sub-case presented more complex calculations, with time dependent variables such as density and the inlet temperature. An unsteady, turbulent flow was considered for the simulation.
6. Simplified-nuclear vessel
For this case, I used the same geometry and mesh from case 1 (Shear-driven cavity flow), and ran a CFD Simulation in Code Saturne for a steady-state, viscous, laminar flow with considerations of heat transfer, non-slip walls with a combination of imposed heat flux and temperature, symmetry planes, natural convection model, and density as a function of temperature. I examined the output and results files, and analyzed them. Additionally, I visually and quantitatively compared the case results with available data.
5. Heated Square Cavity Flow
4. Fluid-Structure Interaction
This case focuses on the numerical simulation of the transverse response of an elastically mounted cylinder subjected to vortex-induced vibrations (VIV). The flow is uniform and the mechanical dynamics of the cylinder is modeled by a simple mass-spring system. The Reynolds number based on the cylinder diameter is taken to be 100 so that the flow is laminar and a 2D calculation may then be able to capture the whole features of the phenomenon. The calculation domain is 2D with only one cell in spanwise direction. Three sub-cases were studied: internal coupling, imposed mesh displacement and imposed mesh velocity.
​
Working this case I learned how to use the main features of Code Saturne for fluid-structure interaction calculations. Specifically, how to perform a calculation on a mobile mesh using the ALE (Arbitrary Lagrangian-Eulerian) frame-work; how to consider the mesh deformation and properly define the parameters of the boundary conditions for a mobile mesh; how to link a solid body in the fluid domain to a mass-spring system with fluid-structure coupling; and how to perform some basic post-processing related to such calculations.
7. T-junction: Turbulent Mixing
This case focuses on modeling a T-Junction and is interesting because in Power plants, thermal fatigue can occur in energy cooling systems which are subjected to cyclic stresses. These cyclic stresses are generally found in T-Junctions where cold and hot water streams mix and the resulting turbulent fluctuations create thermal fluctuations at the walls.
I created the computational domain and a hexahedral mesh for the T-junction with SALOME. Then, I ran an unsteady, viscous, turbulent, CFD simulation with variable fluid properties and no-slip walls, using Code Saturne.
8.Fluid-Dynamics & Solid-Heat Transfer coupling
This case is about a natural convection inside a sheath with different electric wires, and the main objective was to learn how to use the Code Saturne coupling with a thermal conduction and radiation code SYRTHES on a simplified 2D problem.
​
The 2D configuration is a simplification of the real 3D geometry of the wires inside an electric sheath. The 3 disks inside, which are warmer than the air flow, generate a temperature difference creating a fluid movement. The warmer air flow is moving to the top and the colder air flow to the bottom of the fluid domain.
​
For the fluid domain, there are two symmetry conditions and walls conditions imposed to the faces coupling with the solid domain. There is no velocity imposed to create movement inside the fluid area and gravity force was taken into account, as well as a density which is variable in function of the temperature for the air flow.
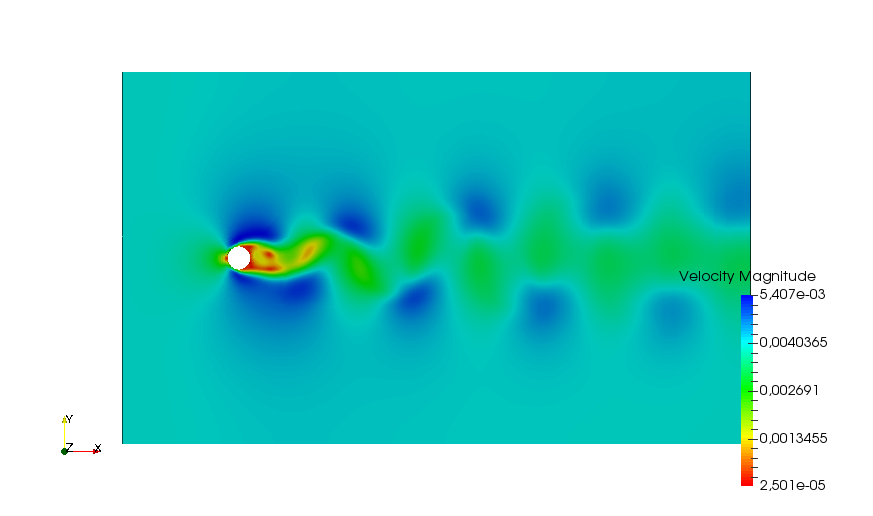


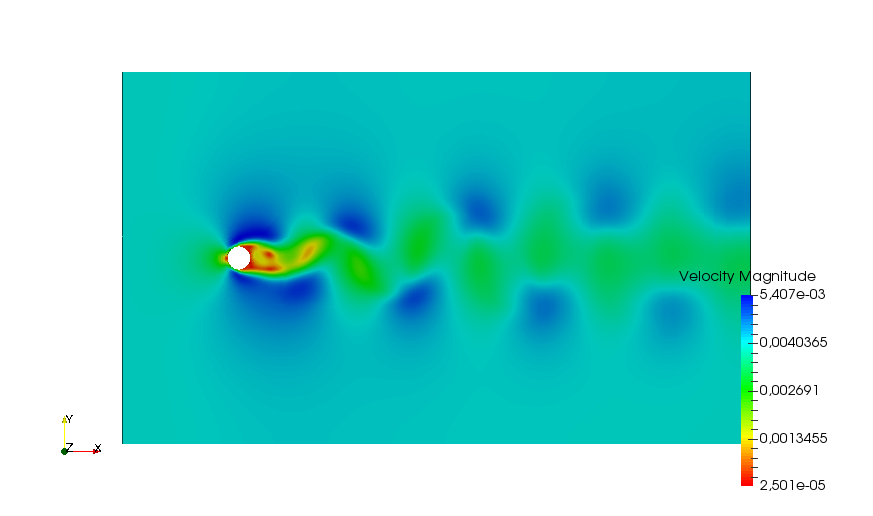
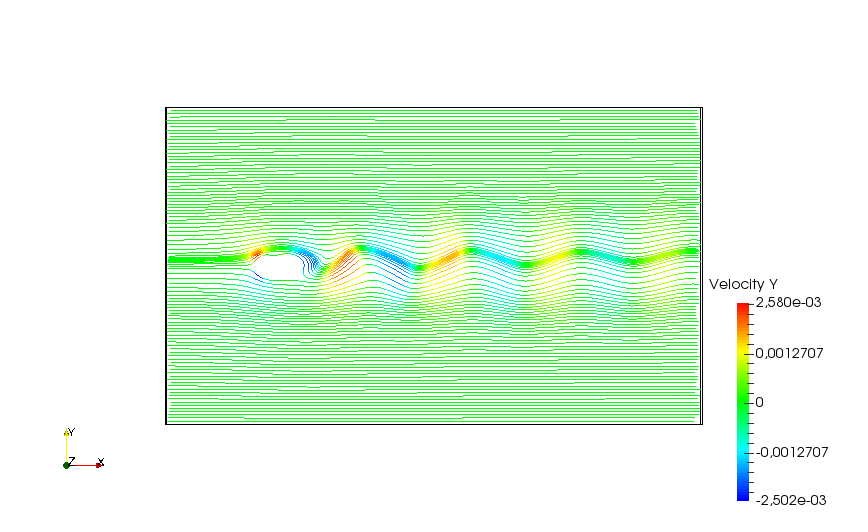
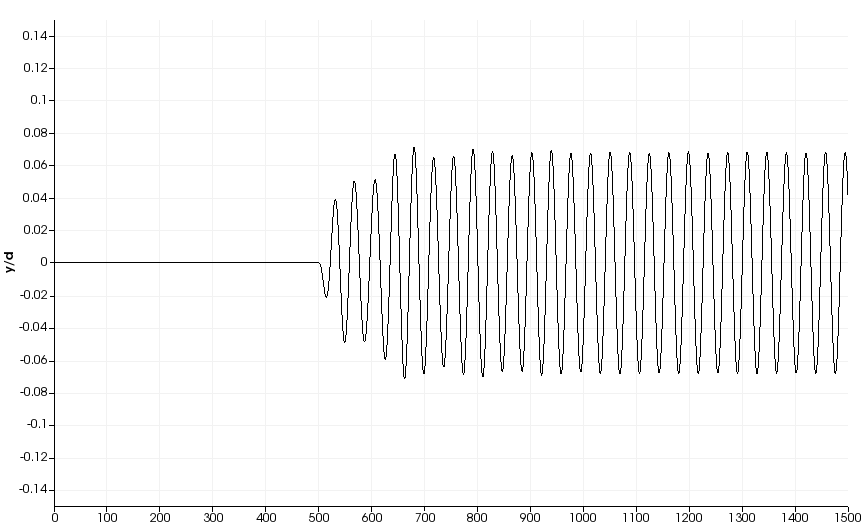

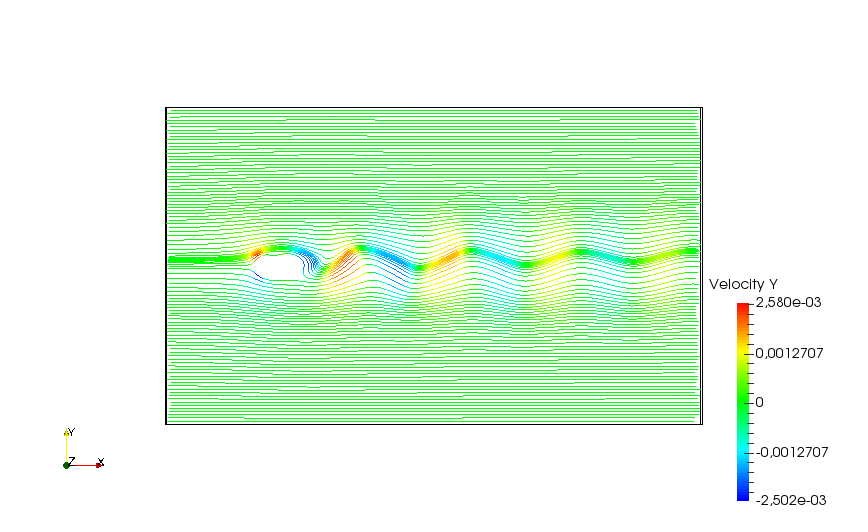

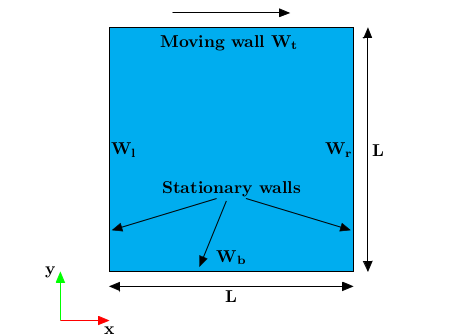
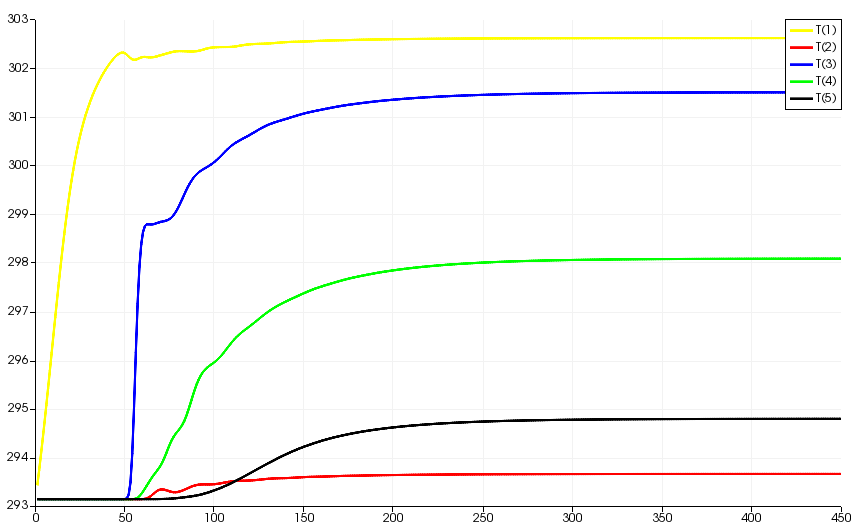



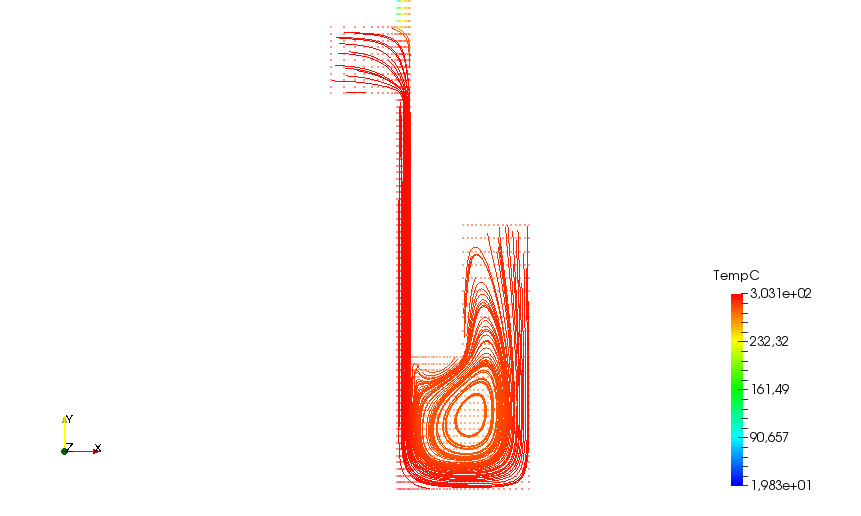

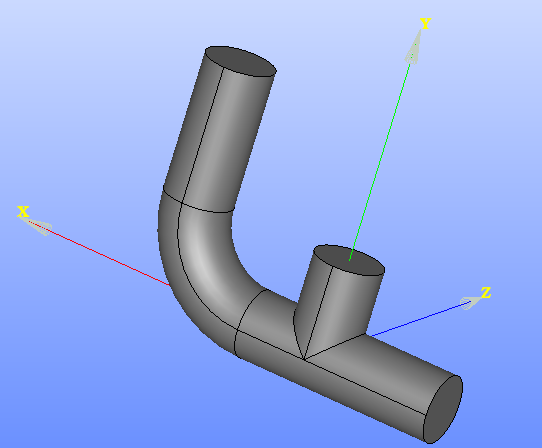


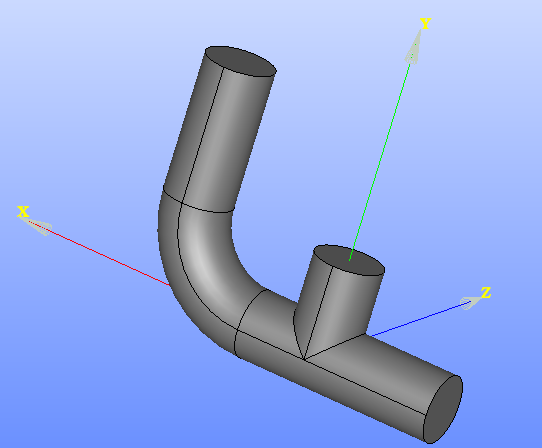

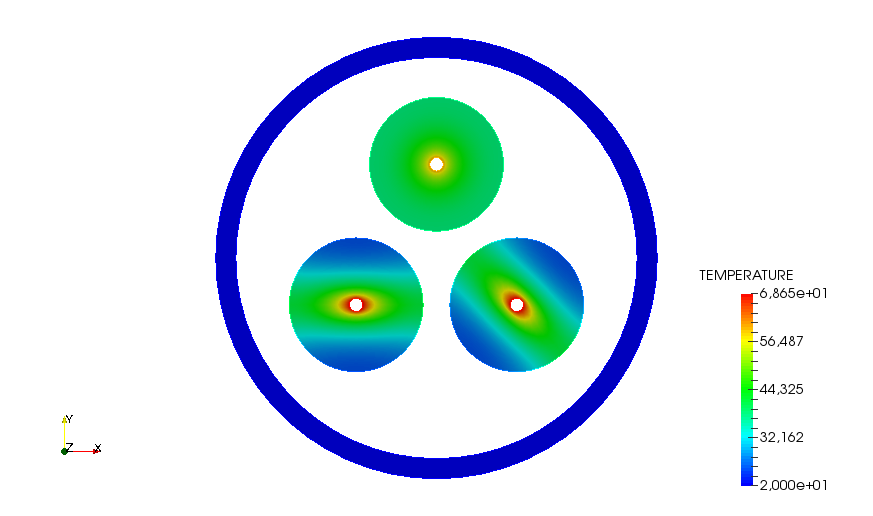


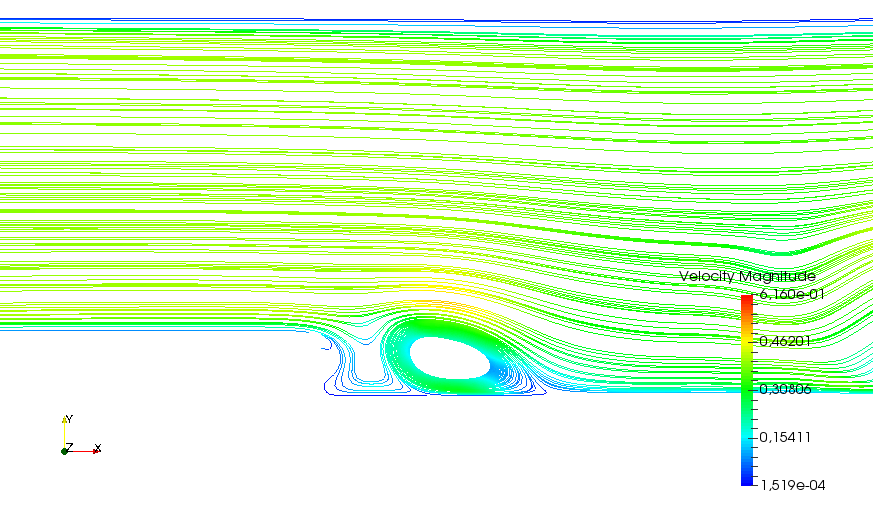


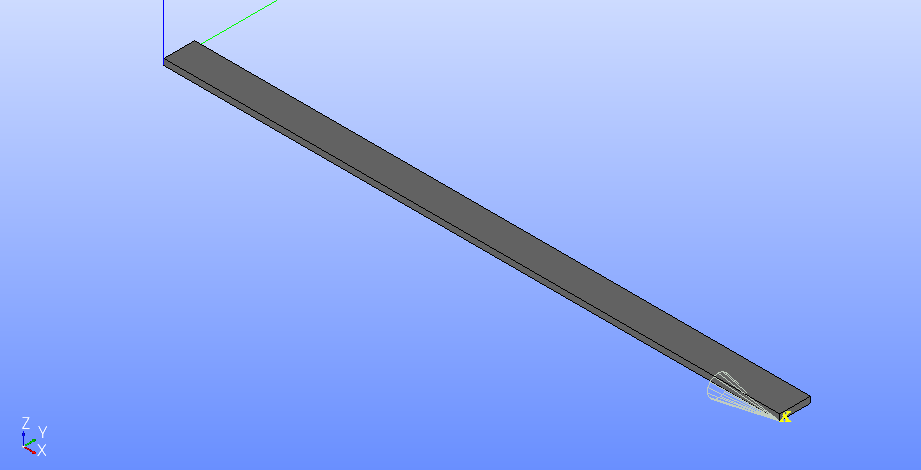
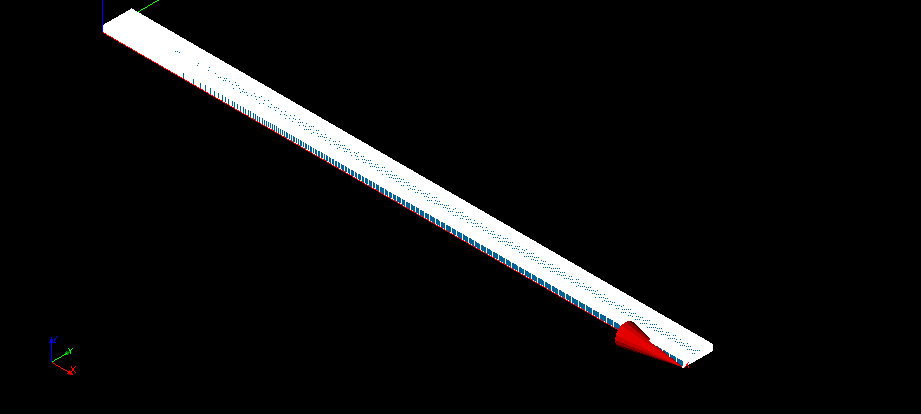

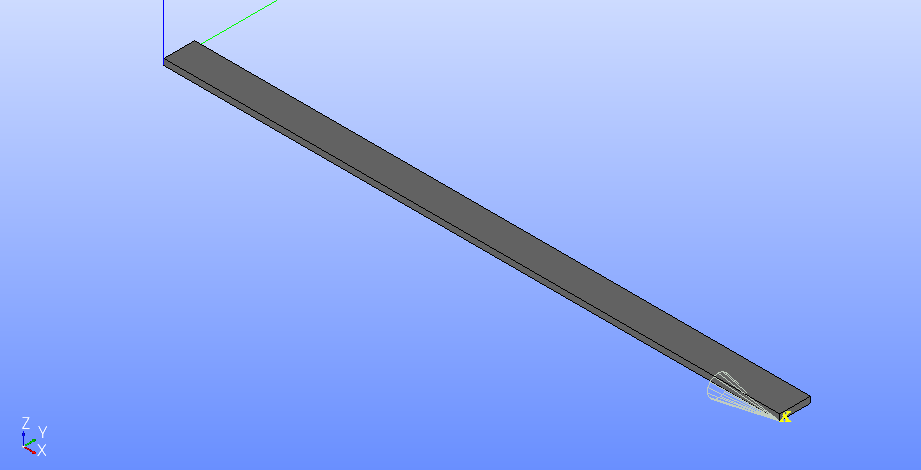
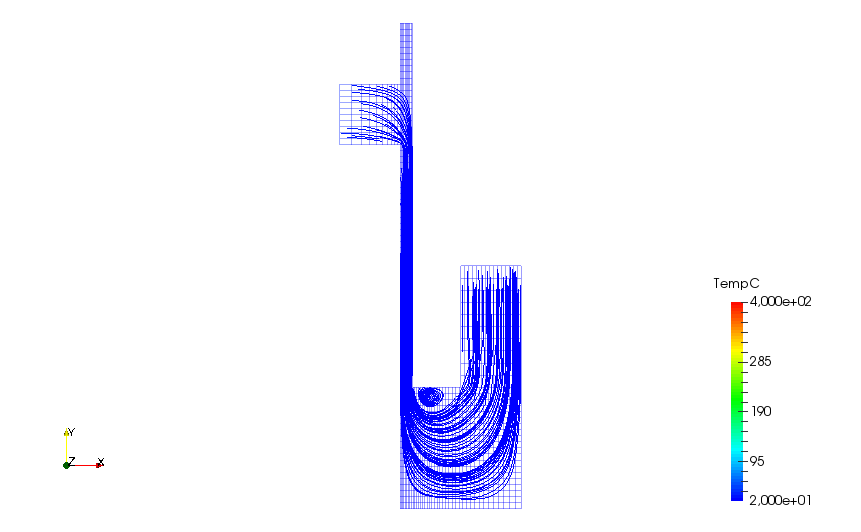


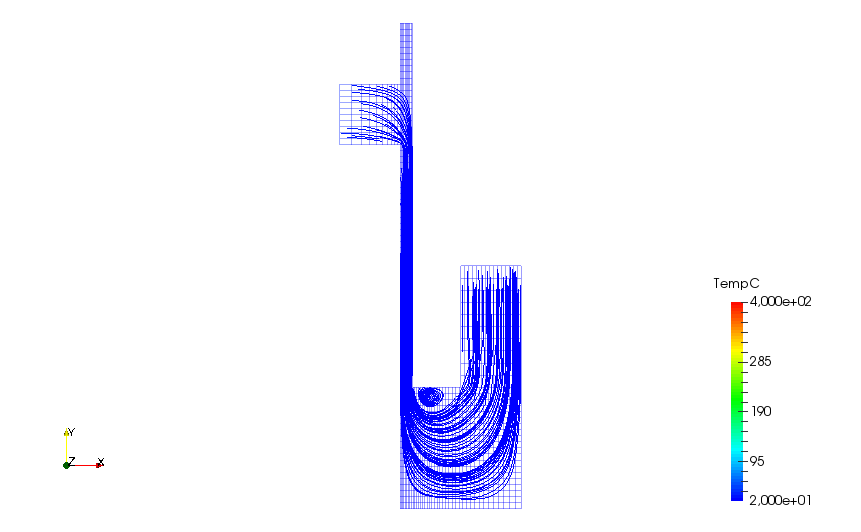
1. Shear-driven cavity flow

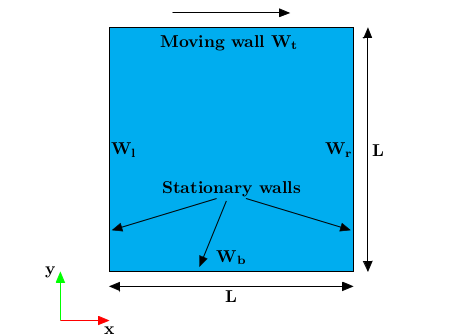

