Building an Air Compressor

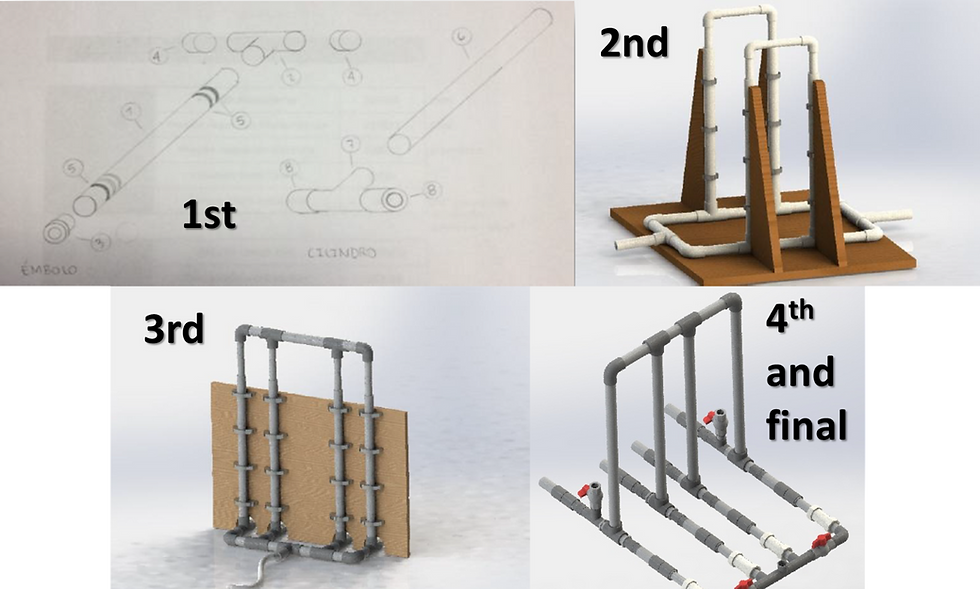


Building Project
An air compressor is a tool that uses mechanical energy and transforms it into pneumatic energy, by compressing air and containing it at a certain pressure so it can be used it for an specific application, like inflation of an automobile´s tire, for example.
​
This was the main project of the Volumetric Machines course of my university. It consisted of the manufacture of a manual operation air compressor, made by a group of 10 people for 10 weeks.
The compressor had to be designed in such a way that it could inflate in less than 2 1/2 minutes a size R13 tire, from an internal pressure of 0 psig to 32 psig. The project was very productive academically, because included activities of calculations, prototype designs till arriving at the definitive design, as well as the elaboration of a budget and of course, the manufacture of the air compressor.
This project required several activities, so the first thing we did was to assign responsibilities like Group Leader, and Presentation, Design, Construction, and Finances Manager. And we used a Gantt Diagram to make the schedule of activities and deadlines.
​
First we did an initial test with a simple manual inflator, to take into consideration the time and force needed to inflate the desired tire. According to our analysis, we drafted several prototypes and discussed their viability with our professor, till we arrived to the chosen one. The 3D Model of the final prototype was made with SolidWorks, including all the 2D drawings.
​
Our air compressor is a positive piston displacement type, with four pistons connected in parallel. In addition the system has eight valves, so each piston cylinder has connected its respective suction and discharge check valve. The discharge valves are connected to the same outlet, so the compressed air can be directed to the tire through the worm blower.
​
As the pistons rise, the pressure in the cylinders decreases and they draw air at atmospheric pressure through the suction valves. In the downward movement, the pressure increases in the cylinders, and once it exceeds the pressure of the tire, the discharge valves open and allow the exit of the compressed air. While this cycle is repeated, compressed air enters the tire and increases its pressure.
​
The compressor has a two-piston release mechanism, so when the pressure increases and the force produced by the four pistons becomes too large for the operator, the inflation becomes less difficult. Therefore, two cylinders are connected directly to the atmosphere with ball valves. When these valves open, they only charge and discharge air to the environment, without producing resistance force.
​
We also included a mechanism to easily disconnect the side pistons, using two ball valves connected in the discharge side. This was due to possible problems that may occur during the stage of development of the compressor, either leaks or defective elements, among others. With this mechanism it is possible to isolate the pistons that are failing by disconnecting them, so the compressor can keep operating with the central cylinders while the problem is solved.
​
September - December 2016











